|
UCM's current operations
are located at Two Bull Ridge where three seams of coal 2-40 feet thick
go down about 300 feet. The first step is to remove overburden (the surface
soil covering the coal). This is a tremendous job that can only be accomplished
using equally tremendous equipment.
Both overburden and
coal are very difficult to excavate. Light blasting is done in order to
loosen both materials before they are handled. UCM uses a mixture of ammonium
nitrate and diesel fuel which is transported, mixed and loaded into each
drill hole by a specially designed powder truck. Typically, there are
anywhere between 20-400 holes in a blast. [click
here to view the 1.1MB video]
UCM's
trump card is the Bucyrus-Erie 1300W Walking Dragline, nicknamed "Ace-in-the-Hole."
This 2100 ton machine arrived in parts on 26 railcars and 40 trucks in
December 1977. It took 11 months to assembl.! The 325-foot beam has a
reach of 270 feet. The bucket
holds 33 cubic yards of material and 35,000 yards of dirt can be removed
within 24 hours. The dragline crew consists of one operator and one relief.
They rotate positions every hour to keep them at their sharpest concentration.
when they aren't at the controls, they do maintenance and repairs on the
dragline. [click
here to view the 4.5MB video]
The
coal is then loaded into trucks using O&K hydraulic shovels. One of
the shovels, an O&K
RH170, will load a 150-ton Caterpillar haul truck in four passes.
It is the largest hydraulic shovel in Alaska. The 150-ton Caterpillar
haul trucks weigh 250,000 pounds and the payload is 300,000 pounds. The
exhaust on the trucks was also factory modified to run through the beds
and keep them heated in the winter. This prevents freezing of the material
to the bed. Other quipment includes several Capterpillar dozers (D10,
D11R, D9, D6 and a D11N which is one of the world's largest tracked dozers),
two Caterpillar loaders (992C and a 994D), and dust control provided by
a 75-ton water truck and two Caterpillar graders (16G and 16H).
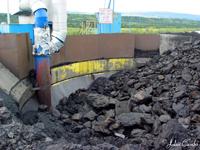 Next,
the coal is trans-ported to the east side of the Nenana River where it
is dumped into a 65-foot deep, cone-shaped hopper. The crusher operates
underneath the hopper and can crush 1000 tons of coal per hour. After
the coal is crushed, it goes through a tube known as the cam span, on
a conveyor belt across the river and into a building on the west side,
called the A-frame. The A-frame can store up to 7,500 tons of coal (one
train's worth) and sits on a 50-foot gravel pad that has a tunnel under
it. While the rain passes through the tunnel at 1/2 mile per hour, the
cars are gravity feed.
The railroad then delivers the coal to
its customers. Coal bound for Korea or Chile travels south to the 34-acre
Seward Loading Facility. This facility is designed to unload coal from
railcars, convey it to storage, reclaim material from storage and load
it onto bulk ships. The stockpile loading rate is currently 3,000 tons
per hour while the ship loading rate is 1,200 tons per hour. The annual
throughput capacity is 3 million metric tons. As of June 14, 2005 two
trains arrive at the facility, each with a 75 coal hopper consist.
|