|
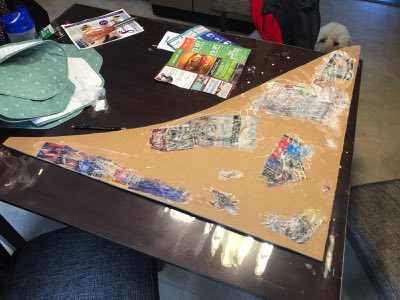 |
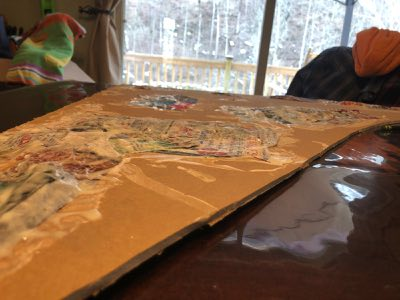 |
As Mike Cooper and I initially discussed the creation of the layout we decided to create removable foam board around the tracks to facilitate easier scenery work for my limited reach. Who would have thought we could send a scenery board with John and Leigh to work on at their home in Kentucky! They are constructing a Woodland Scenics Maple Leaf Cemetery kit with a few fun additions. John is shown here cutting out the various pieces of the basswood tool shed. |
Although the foam board is flat true life dictates otherwise. John and Leigh use newspaper to create slight rises in the scene.
"Every project needs a foreman!", says John as Zeus peeks a supervising eye up over the table. Rumor has it he is actually looking for a table snack, but his press secretary released a statement he is actually keeping a watchful eye on the workers. |
Here is another view of the land form work. Knowing John and Leigh's propensity to dark humor it will be interesting to view the finished product. Will there be Walking Dead? A leg bone sticking out of a grave with a dog yanking on it? Or maybe something as simple as representations of themselves working a funeral? |
|
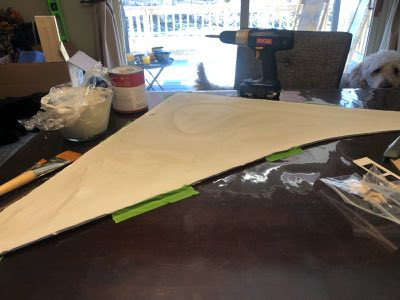 |
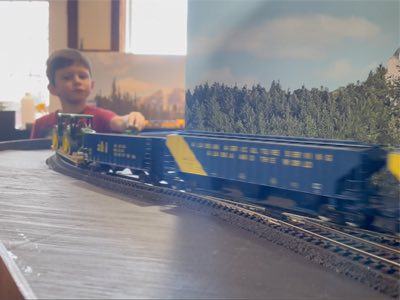 |
Leigh has done her share of mortuary facial reconstructions using a wide variety of waxes. She applies her skills here to model landscapes using high quality Liquitex Flexible Modeling Paste. This paste is easy to work with and holds great form. With an artist flair Leigh smooths the paste over the land forms. |
The finished preparation work looks great! Zeus, the ever vigilant foreman, nods his head in agreement. "Time for pizza", he exclaims! |
Over the weekend the entire family drops by to celebrate Terry's birthday. Four grandsons spend 4-5 hours watching the trains roll past the new scenic backdrops. Oldest grandson Liam took the controls and ran several trains, blowing the horn and ringing the electronic bell. He also enjoyed following the train with his great grandfather Doug's John Deere farm tractor. |
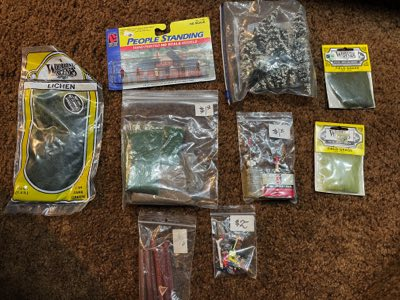 |
|
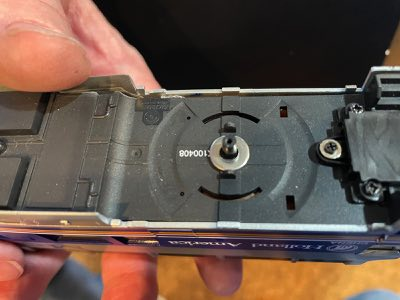 |
Terry is a devotee of garage and estate sales. She happened upon a huge estate sale near our home and found a large collection of HO scale buildings, freight cars, locomotives and scenic materials. I returned with her and found a few items I could use. The seller gave us everything for half price. |
For train night, Jackie brought iced and chocolate chip cookies for Terry's birthday. This was a great finale to the chicken sandwiches, homemade French fries and salad bar. |
Over the past week Rick added #6 washers to five Princess and two Holland America passenger cars plus one Alaska Railroad baggage car. These modification brought the rail car's couplers up to NMRA standards. |
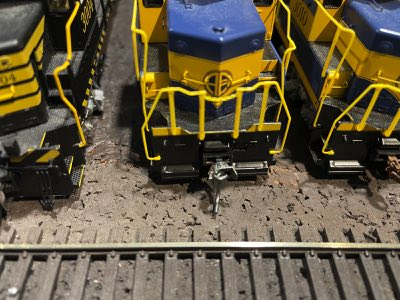 |
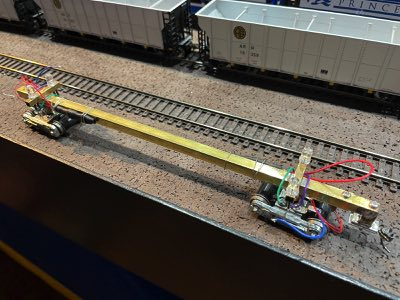 |
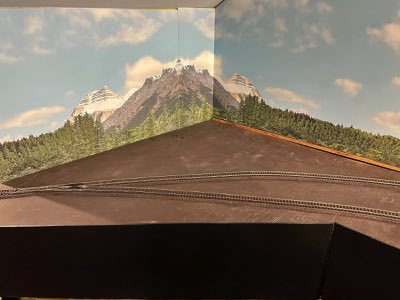 |
Somehow the front coupler on GP40 #3009 got broken so Rick installed a replacement. As it turned out one of the hostlers was talking on his cell phone to his girlfriend and stopped paying attention to what he was doing. He now works at McDonalds just down the road. |
Rick is working on a custom built track testing car. There are LEDs on the front and back plus on each side. This car mimics the electrical connections a locomotive experiences as it crosses over switches or other areas of interest. Next week Rick will give it a test run on the layout |
This piece of plywood was added when the reverse curve was eliminated at the "dreaded S curve." Unfortunately, at the southeast end of the plywood an elevation break was created. The rise of this sheet of plywood butted up against the level area of the next piece of plywood. This explains the recent rash of "pull aparts" at this location. |
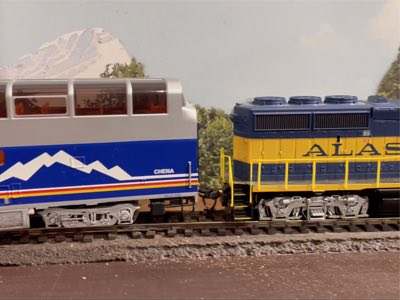 |
|
|
This video shows the change of coupler heights as the train travels across this new piece of plywood. Small changes are okay, but the large change at the end of the video is the location of the extreme elevation change and subsequent "pull aparts." My apologies for the occasional camera shake due to walking along side the train.
Next week we will rip up 16 inches of track and cork road bed on either side of the elevation break, apply a belt sander to the region and then lay new cork bed and track. The main line will be down for two weeks. |
|
|